1月2日,新年伊始,在深江铁路建设建设现场,一架900吨的“巨无霸”智能化移动模架惊艳现身,成为工程建设的顶梁柱,这正是来自襄阳的企业中铁十一局汉江重工有限公司(简称汉江重工)的“年度力作”。
深江铁路是国家“八纵八横”高速铁路网中沿海通道的重要组成部分,途经深圳、广州、东莞、中山、江门5个地市,线路全长 116 公里。该铁路7标标段内有滨海湾特大桥、沙角特大桥、沿江高速特大桥三座大桥工程,情况复杂,如果仅仅采用传统的支架现浇工艺施工,不但存在极大安全风险,而且无法保证工期。
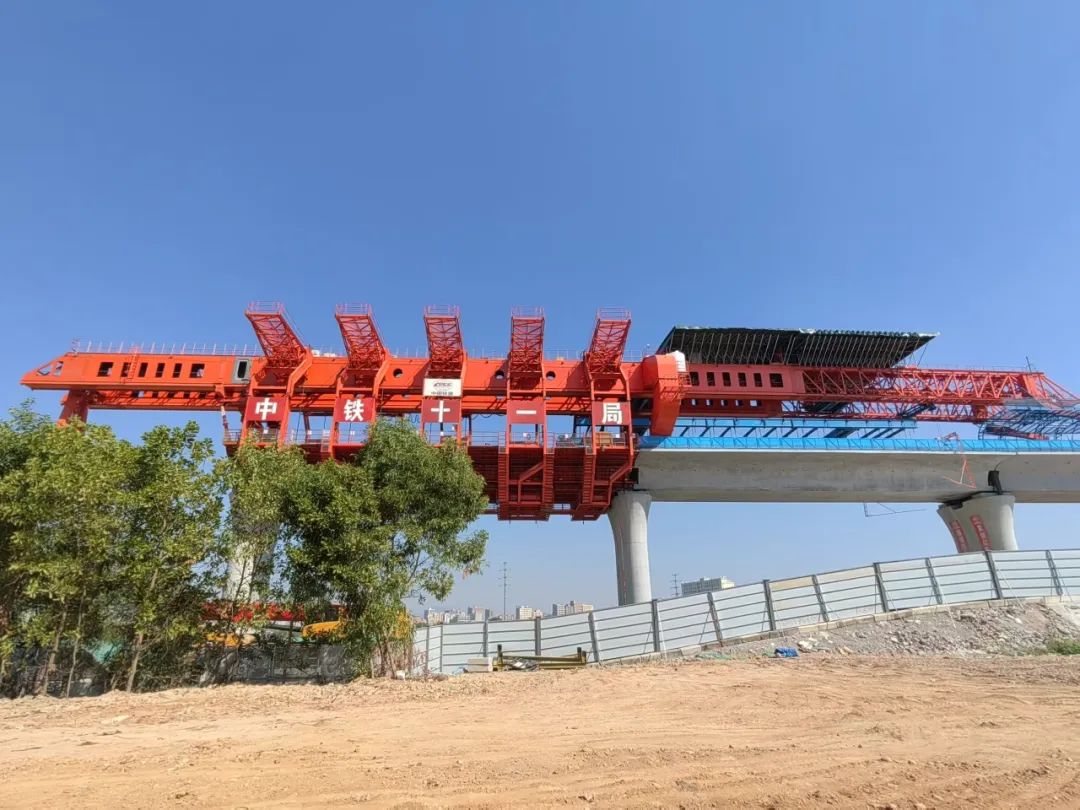
“为保质保量建设深江高铁,我们研发团队将重点聚焦到‘智造’施工上。”汉江重工装备制造厂总工程师李满说,“以往混凝土振捣环节都是人工操作,施工环境艰苦,精度也难以控制。为解决这一问题,我们研发采用自动化辅助振捣控制系统,通过工控机或操作台控制振捣器工作,实现对混凝土振捣的精确控制,大幅提升了混凝土的密实性和抗渗性。浇筑混凝土前,只需设定好振捣时间、振捣间距、振捣点位、分层厚度等参数,开启控制振捣器单、联动,进行辅助振捣,使混凝土整体成型质量更好,内实外美。”
深江铁路7标项目毗邻龙涌,施工容易受台风、强降雨、曝晒等恶劣天气的影响,这是设计时必须解决的问题。经过多次现场考察调研和方案综合比选后,汉江重工研发团队创造性地研发智能雨棚控制系统,通过多功能传感器,获取设备风速、雨量、温度等数据,操作员读取数据后,轻轻一点便可展开或收缩雨棚,遮阳防雨两不误,提升了设备工作全天候作业能力,使“在风雨里建桥梁”也具备了可行性。
“要想让这个900吨的‘大家伙’战斗力时刻‘在线’,精心呵护每一件装备势在必行。”李满介绍,汉江重工研发团队引入自动喷淋养护系统,通过手机终端远程控制喷淋养护过程,实现箱梁的梁面、梁侧面、底面、梁内的定时喷淋及温湿度检测喷淋,既保障了工程质量,又践行了低碳环保的施工理念。除此之外,它还可以根据预设的养护计划,自动调整喷淋时间和强度,确保每一片桥梁预制构件都能得到均匀、充足的养护,为梁场提供准确、可靠的养护数据支持,为桥梁建设的质量控制和风险评估提供有力保障。
“模架设计与制造、桥梁施工过程中均存在尺寸、荷载的不确定性,要准确预测移动模架的应力,并保证结构绝对安全存在一定难度。”李满说,为克服这一系列难题,汉江重工研发团队聚焦先进的监测技术,研发了综合智能监控技术,通过应力应变计、激光测距仪等多种监测装置与智能云平台系统的协同使用,实现移动模架施工过程中支腿、C型吊挂、已浇筑梁体、过孔状态等全方位自动化监测与可视化展示,并能够实时预警、在线运维,实现设备控制系统智慧升级,提高移动模架自动化与智能化水平。施工时,它会对桥梁施工过程中模架结构运行数据进行实时采集,获取模架运行安全状态信息,确保桥梁施工安全,摇身一变成为新一代智能“安全卫士”。
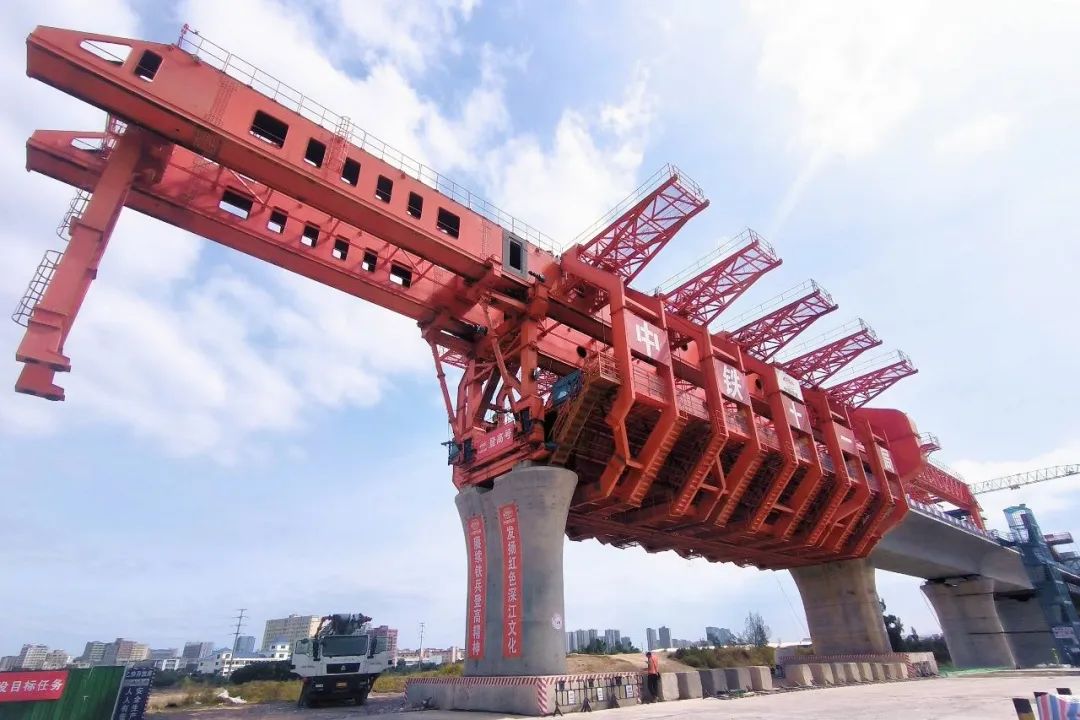
发展新质生产力是推动高质量发展的内在要求和重要着力点,更为汉江重工指引了前行的方向,一批批设备落地推进,一项项技术走向市场,一个个品牌拔节生长,一群群产业聚沙成塔,交出了一份“汉江答卷”。
汉江重工装备制造厂党支部书记林少亮介绍,企业的研发团队还在工艺工法上进行了一系列创新,让更多“智能”设备变得更加“智慧”。研发的集卸料、钢筋绑扎和浇筑为一条生产线的两跨移动模架,采用后方导梁自平衡过孔、前支腿防倾覆、中支腿对位调整机构,突破了将钢筋绑扎分离在设备体外的技术难题,首次实现了钢筋整体绑扎与现浇并行桥位制梁施工设备,也解决了多跨长结构适应小曲线施工;通过“钢筋捆料机械化卸车、送料,钢筋笼整体绑扎,整体吊装入模的设备及工法”完整流程创新技术,使现浇梁施工中钢筋笼绑扎与浇筑养生工序从串序施工变成并行施工,从而使每孔施工时间缩短5天左右,使移动模架施工效率提高25%以上……培育新质生产力,开拓发展新赛道,未来,汉江重工将立足科技发展前沿,持续加强关键核心技术攻关,纵深推进科技成果应用转化,以新质生产力赋能企业高质量发展取得新成效。